Steel is the most commonly used metal in the world, finding use in components, products, and structures across a wide range of industries. This popularity is largely due to the material’s inherent strength, hardness, and durability. However, when considering steel as a material for a manufacturing project, it is important to note that steel is not a single metal but rather an umbrella term for a group of metals consisting of primarily iron and carbon, and often various amounts of other elements. It is available in numerous variations, each of which features a slightly different composition and exhibits a slightly different set of characteristics, which make it suitable for different applications.
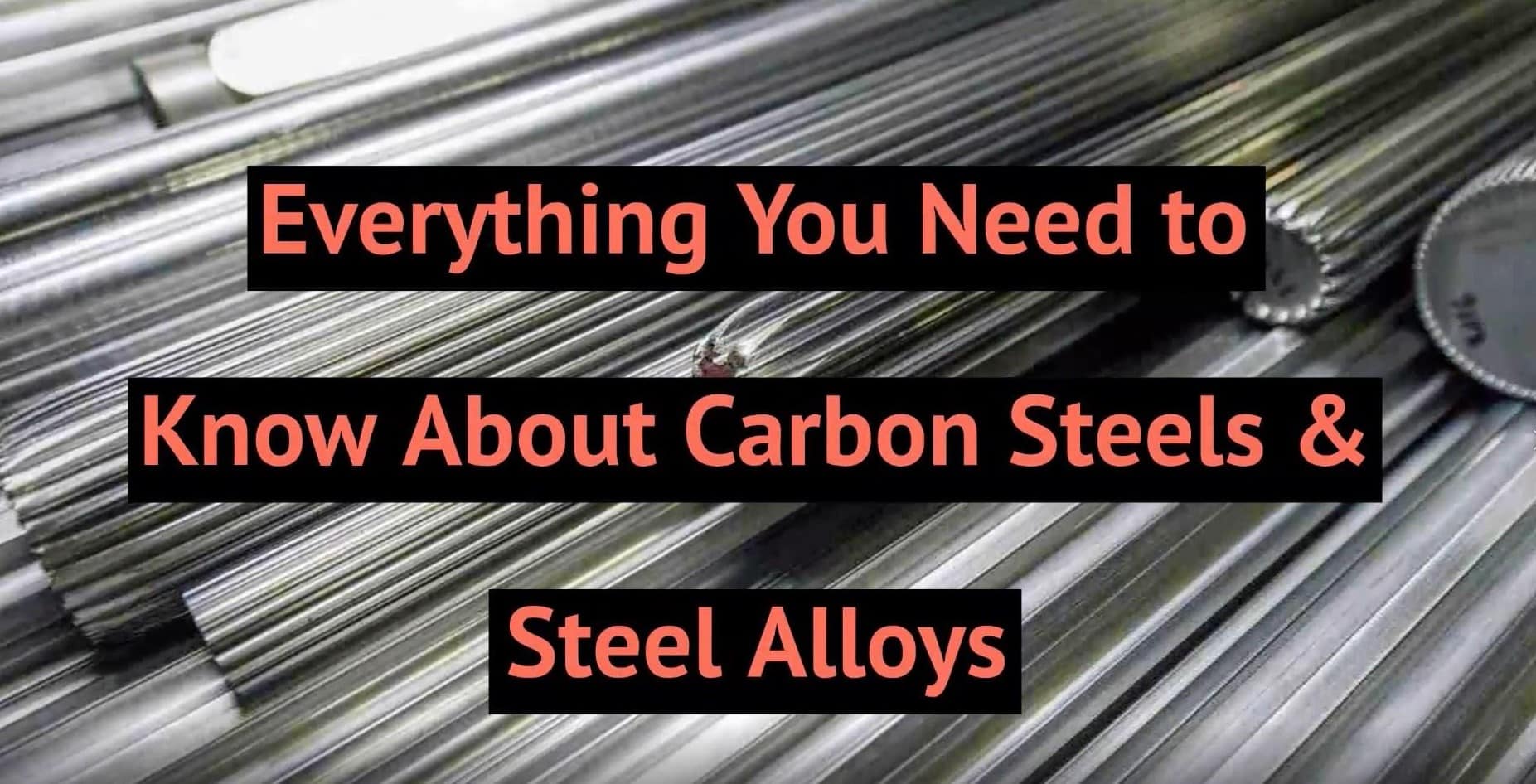
By some accounts, there are over 3,500 types of steel available. This broad selection makes it possible for industry professionals to find a steel that matches their exact needs, but also makes it more difficult to select the right one. In the following guide, we provide an overview of everything you need to know about carbon steel and steel alloys. It discusses what steel is, the types available, and the typical applications of the material to help readers attain a better understanding of steel and how to determine which one is right for a project.
What Is Steel?
Steel is an alloy of iron and carbon. Its primary constituent—iron—is very weak and soft in its pure form. Adding carbon to the element significantly increases its tensile strength, hardness, and resistance to wear and abrasion but lowers its ductility, machinability, and toughness. However, the total amount added must be less than 2% for the resulting metal to be classified as steel. Metal with carbon contents greater than 2% is classified as cast iron.
In addition to carbon, other elements can be incorporated during the steel-making process to enhance the steel’s characteristics even further. If the steel contains by weight one or more alloying elements to a standardized percentage, it is then classified as alloy steel. The exact properties exhibited by particular alloy steel are dependent on the elements included and their proportions. In general, alloy steels demonstrate immense strength, hardness, and versatility. Additionally, they are highly recyclable, allowing industry professionals to reuse and repurpose them over and over without a loss of material strength or quality.
Carbon Steels
Carbon steels consist primarily of iron and carbon and which relies on carbon as the principle hardening element. They are commonly grouped into three subcategories: low-carbon steel (0.03% to 0.15% carbon), medium-carbon steel (0.25% to 0.50% carbon), and high-carbon steel (0.55% to 1.10% carbon). The higher the carbon content, the harder the resulting material and, consequently, the harder it is to work. For this reason, low-carbon steels are more commonly used than high-carbon steels in manufacturing operations.
Steel Alloys
Steel Alloys combine carbon steel with other alloying elements to add or enhance specific material characteristics, such as strength, hardness, or corrosion resistance. They can be grouped by alloy or alloy percentage. High-alloy steels contain a higher percentage of alloying elements (above 8% but typically at least 10%), while low-alloy steels contain a low percentage of alloying elements (generally between 1% to 5% but can have up to 8%). Steel alloy properties are heavily influenced by the alloying elements added. Some common alloying elements are listed below.
- Chromium
- Cobalt
- Copper
- Manganese
- Molybdenum
- Nickel
- Silicon
- Tungsten
Grading Steel
In addition to composition, there are many other factors that influence the characteristics exhibited by a steel alloy. Various standards organizations have developed grading systems to provide methods of categorizing carbon steels and steel alloys by all of these factors. In the United States AISI (American Iron and Steel Institute), SAE (Society of Automotive Engineers) and ASTM (American Society for Testing and Materials) are commonly used.
- The AISI/SAE grading systems utilize a unified numbering system (UNS). Each metal is assigned a four-digit number with the first two digits indicating its steel type and alloying element concentration and the last two digits indicating its carbon concentration.
- The ASTM grading system also utilizes a UNS classification for metals. Each metal is assigned a letter designating its overall category (A is used for iron and steel materials) and a number corresponding to its specific properties.
Applications & Benefits of Carbon Steels and Steel Alloys
Steel alloys demonstrate excellent strength, durability, and, depending on what they are made of and how they were made, numerous other advantageous characteristics. These qualities make them an ideal material choice for many manufacturing and construction projects. Typical uses for steel alloys include:
- Construction materials (e.g., bars, beams, coils, plates, rods, sheets, wires, fasteners, etc.)
- Automotive and Heavy Equipment (e.g., gears, splines, pulleys, shafts, rotors, etc.)
- Oil and Gas (e.g., Pipes, tubes, fittings, tanks, etc.)
- Mining (e.g., machinery, drills, tooling, etc.)
- Manufacturing/Machine tools (e.g., dies, molds, conveyors, etc.)
- Hand Tools (e.g., wrenches, screwdrivers, sockets, etc.)
Custom Steel Spline Shafts, Spur Gears, and More From Grob Inc.
Carbon steel and steel alloys are used to make a wide range of parts and products. The experts at Grob Inc. use it to produce a variety of cold-formed products, including spline shafts, spur gears, timing belt pulleys, and more. To learn more about the cold forming capabilities at Grob, check out the cold-formed products page. Contact us today to discuss your cold forming needs with one of our experts.